Hřídel setrvačky
Stručný popis
Hřídel setrvačky je ocelová součást válcového charakteru, která ve strojku NH vykonává rotační vratný pohyb a slouží k nesení dvojkotouče s popudným kamenem, a jádra vlásku s vláskem a setrvačníkem. Hřídel je na svých koncích - čepech uzpůsobena k uložení v kluzných ložiscích, kde jsou přenášeny radiální a axiální reakce sil vybuzené:
- účinkem sil od hmotnosti sestavy hřídele s nesenými prvky
- chodem mechanismu
- rázy, například při pádu hodinek na zem.
Maximální rozměry hřídele u kalibru 50: délka l = 2,85 mm a ø 1,3 mm. Těmito malými rozměry, členitostí povrchu a požadavky na přesnost se řadí mezi součásti náročné na výrobu a zároveň je označována jako nejnamáhanější součást náramkových hodinek – ony čepy hřídele uložené v ložiscích.
Funkční části hřídele
Na prvním obrázku je vyobrazena samotná hřídel v poloze hodinek zadní stranou nahoru, čepy nejsou uzpůsobeny pro tlumič nárazů ( Elast-blok, KIF anebo INCABLOC ).
Červenou barvou jsou označené čelní kruhové plochy přenášející axiální síly z hřídele do ložisek a fialovou barvou válcové plochy přenášející radiální síly z hřídele do ložisek. Na tento typ ploch je kladen veliký důraz na přesnost výroby, protože se jedná o plochy za chodu funkční v kterých se odehrává rotačně vratný pohyb soustavy a tím tření mezi hřídelem a ložisky.
Zelenou barvou je označena kuželová plocha na kterou se lisuje dvojkotouč s popudným kamenem. Díra v dvojkotouči je válcová, dřík hřídele kuželový a uložení soustavy je s přesahem – montáž dvojkotouče se tedy provádí lisováním. Při lisování na hřídel se dvojkotouč deformuje – roztahuje – čímž je zaručena jeho aretace. Jako doraz při lisování slouží čelní plocha osazení hřídele – vyznačeno opět zeleně. Pro nalisování a vylisování dvojkotouče je třeba speciálního přípravku.
Modrou barvou jsou označené plochy, na které se lisuje jádro vlásku s vláskem a setrvačník. Anologie uložení, montáže a demontáže je identická jako v předchozím případě.
Pozn.: U některých hřídelí se v modře značené části vyskytoval ještě jeden kuželový dřík, který nesl setrvačník.
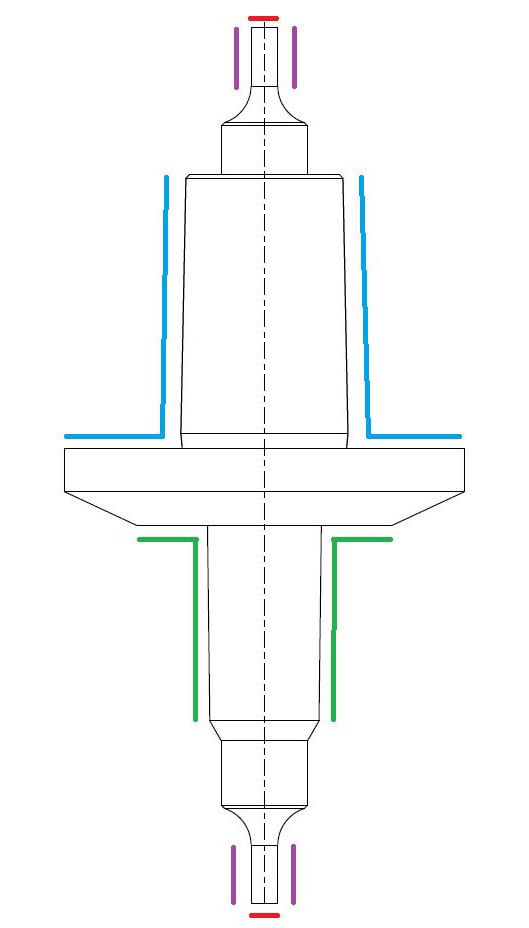
Výroba
Je popsána tak, jak probíhala v letech 1954 / 1994, byť se průběhem let jednotlivé rozměry hřídelí pro jednotlivé typy strojků měnily. Výkresová dokumentace uvedená v textu odpovídá základnímu kalibru 50. Výroba spočívala ve třech výrobně-technologických operacích: soustružení, broušení a leštění ( rolírování ), kdy vstupním polotovarem byla ocelová tyč o průměru 1,3 mm, tzv. hlazenka, dodávaná švédskou firmou SANDVIK. Zhotovení jednotlivých technologických operací probíhalo na jednoúčelových strojích, nastavením určených přímo k dané operaci na součásti.
Soustružení:
Bylo prováděno na automatickém dlouhotočném soustruhu TORNOS M-4 vyráběném ve Švýcarsku stejnojmennou firmou – TORNOS. Automatický v tomto případě neznamená CNC – tedy číslicově řízený, ale automaticky řízený pomocí vaček. Každá vačka, mechanicky spjatá s jedním nožem, byla tvarově uzpůsobena tak, aby po ní odvalující se rolna přenesla informaci o tvaru noži obrábějícímu danou konturu – tvar vačky tedy určuje dráhu nože. Tímto způsobem bylo využíváno až 5 nožů v suportu současně na obrobení jedné součásti, přičemž každý z nožů měl předdefinovánu svoji část k obrobení. Po vyjetí posledního nože z řezu se oddělila vysoustružená součást od polotovaru a proces se opakoval. Pomocí tohoto automatického mechanismu bylo dosaženo vysokého počtu vysoustružených součástí během krátkého časového intervalu v téměř identické kvalitě. Obsuha – kontrola - musela jen v určitých časových úsecích kontrolovat kvalitu obráběcích nožů, aby nedocházelo ke zmetkovitosti vlivem jejich otupení.
Používaný typ soustruhu TORNOS M-4 na obrázku staženém z internetu.
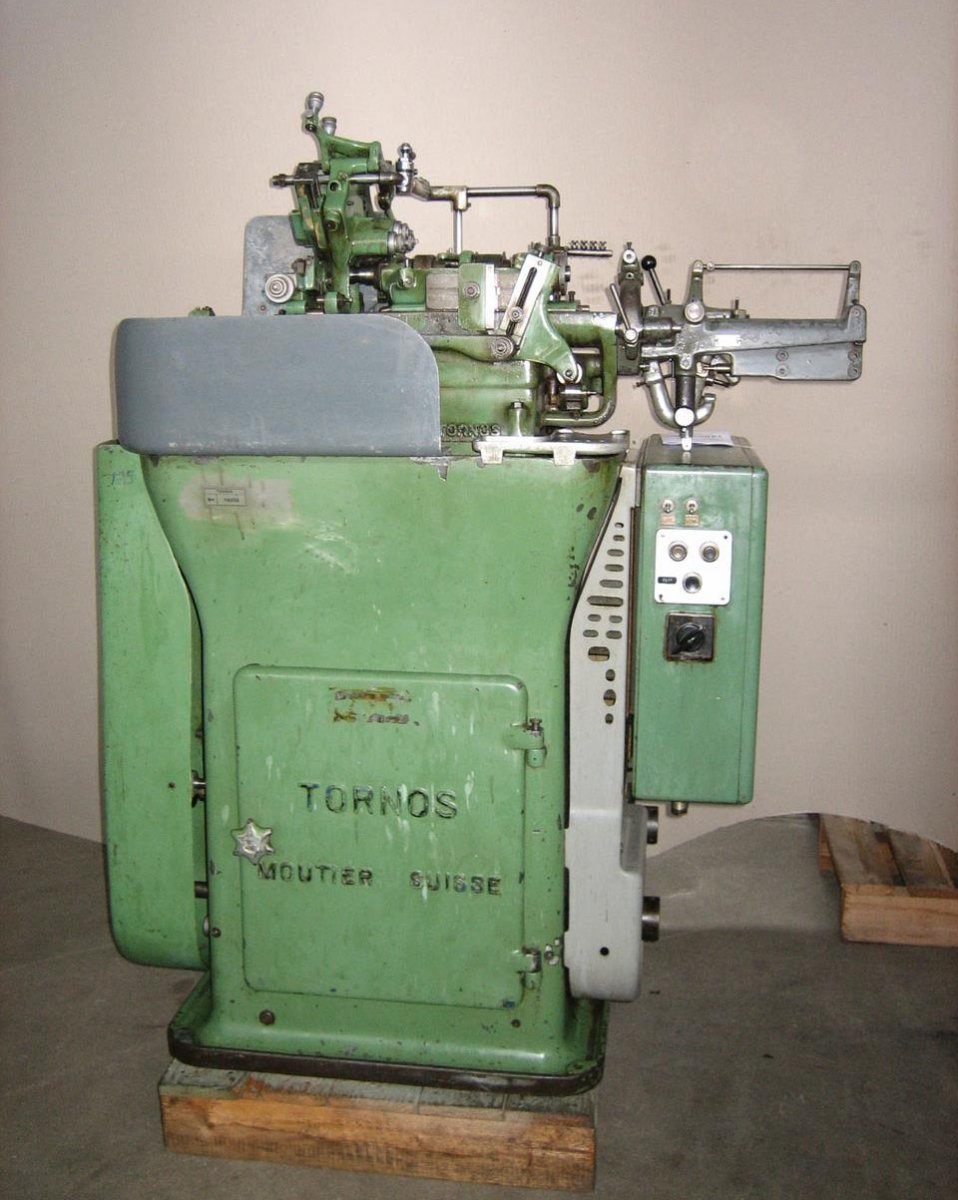
Výsledný produkt soustružení je k vidění na prvním výkrese. Výkresová dokumentace zde prezentovaná je kompletně překreslena z dobové dokumentace zhotovené konstruktéry v Eltonu s tím rozdílem, že nebyla zpracována ručně perem na pauzovací papír, ale ve 3D cadu Pro-E Wildfire 5, kdy se nejprve zhotoví 3D model a posléze 2D výkres. Jako podklad pro její tvorbu posloužila publikace pana Jaroslava Vajsara – viz, použité prameny: 1, Rozmístění kót, detailů, popisků, drsností a tolerancí je beze-změny převzato z původní dokumentace. Font autorova písma není možné ve 3D cadu replikovat.
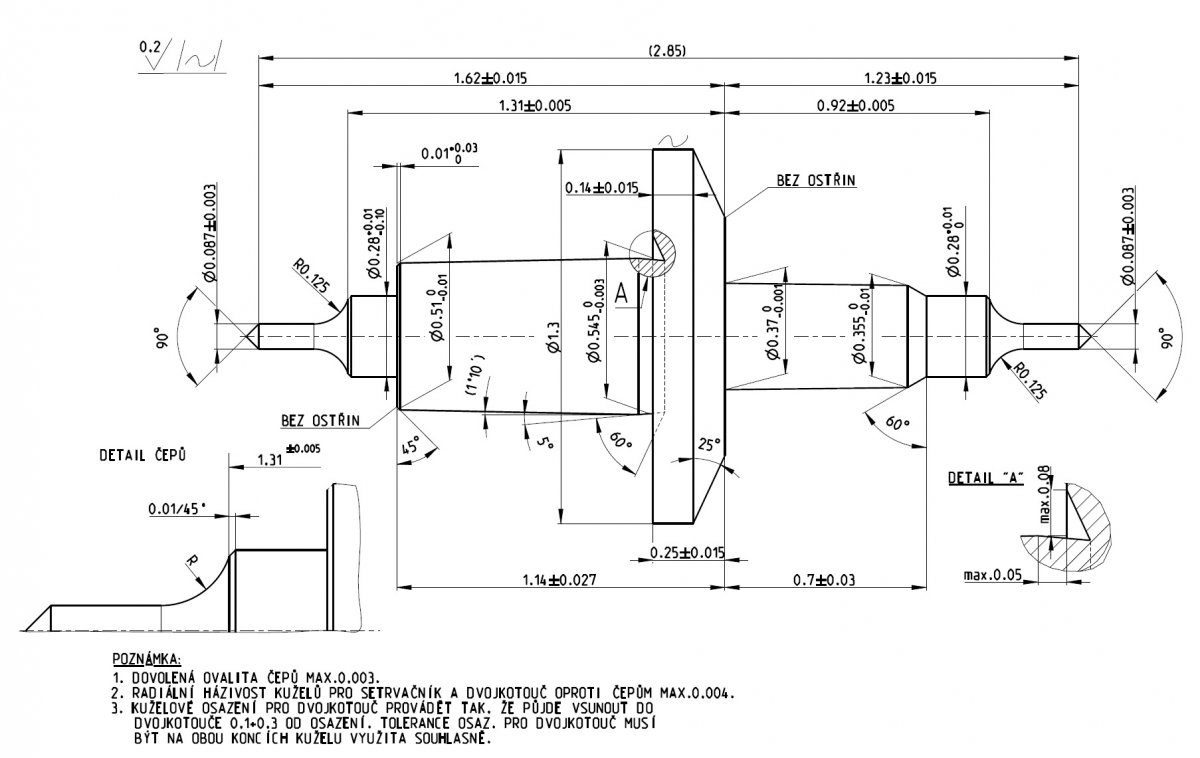
Aby bylo možné součást zobrazit a následně okótovat tak, abychom mohli pozorovat jednotlivé konstrukční prvky, bylo nutné zvolit měřítko 100:1, tedy hřídel 100x zvětšit. Použitý formát výkresu jsem zvolil A3. Bohužel v jakém měřítku a na jakém formátu je zobrazena předloha se mi nepodařilo zjistit, protože mne dostupný podklad postrádá rohové razítko.
Z konstrukčního hlediska stojí za povšimnutí:
1, Použité tolerance – tolerance zde uváděné, jak průměrů tak délek, se pohybují v drtivé většině v řádech setin a tisícin, což je vynuceno miniaturností součásti a požadavku na přesnost. Pro ilustraci se podívejme například na podélný rozměr 1,31 ± 0,005 mm. Při výrobě součástí v přesném a všeobecném strojírenství se používá tolerančí hodnota pro délkový rozměr do 3 mm ± 0,05 mm, což je vztaženo k jemné třídě přesnosti. Střední třída přesnosti už nabízí toleranci ± 0,1 mm a je v běžné výrobě nejpoužívanější. Toleranční pole rozměru na hřídeli je tedy přísnější o jeden desetinný řád, než nejpřísnější běžně užívaná třída. Tato skutečnost klade poměrně vysoké nároky na kvalitu obráběcího stroje a podmínek okolí.
2, Tvar použitého zápichu – DETAIL A.
U hřídelí s velikým poměrem průměrů se standartně používají normalizované zápichy tvaru F a G, které jsou definovány normou, potažmo strojnickými tabulkami, a mají sloužit k rovnoměrnějšímu roznesení napětí koncentrujícímu se u skokových změn průměrů na hřídeli. Každá změna tvaru u standartního zápichu je pro plynulejší tok napětí vylehčena radiusem. Z výkresu našeho hřídele je však patrné pouhé zajetí obráběcím nožem do přechodu z ø 0,545 na ø 1,3 mm, a tím vytvoření ostrého vrubu – koncentrátoru napětí. Tento konstrukčně nestandartní prvek si vysvětluji pouze technologickou náročností výroby, titěrností součástí a faktu, že nejvíce namáhané jsou pouze čepy hřídele uložené v kluzných ložiscích. Protější strana, kde je nalisován dvojkotouč s popudným kamenem je bez zápichu a bez jakéhokoliv ošetření. Stejně je tomu i u přechodu z ø 0,51 na ø 0,28 mm. Nicméně součást od uvedení do výroby stále plní svojí funkci, což je nejpodstatnější.
Broušení konců čepů:
Hřídel opustila vřeteno soustružnického automatu ve stavu s kuželovými zakončeními konců čepů. Tyto tvarové prvky jsou nepřípustné pro chod hřídele v axiálních ložiscích, protože by došlo k jejich vydření a tím rozhození axiálního uložení v sestavě základny strojku a můstku setrvačky. Druhou a zároveň náročnou operací ve výrobě bylo tedy odstranění těchto kuželových konců broušením, které zaručilo jak zrovnoměrnění tření konců hřídele v axiálních ložiscích, tak dodržení dvou podélných funkčních rozměrů daných výkresem. Podélné rozměry mají vliv na uložení hřídele mezi axiálními ložisky – u příliš dlouhé hřídele hrozí znemožnění otáčení a tím i chod hodinek, u příliš krátké hřídele se zvětší vůle mezi ložisky a s tím spojený zbytečný osový chod hřídele.
Součást byla upnuta v přípravku za výchozí funkční plochu A a obsluhou vsouvána mezi dva rotující a podélně nepohyblivé brusné kotouče k opracování. Symboly znaku stříšky ve výkrese značí podepření plochy v přípravku při opracování. Operace byla prováděna na dvou paletových bruskách KIENZLE. Potřeba navyšovat počet vyráběných kusů vedla podnik v průběhu doby k přestavbě stávajících anebo vývoji nových vlastních strojů, které umožňovaly nejprve částečnou a poté zcela automatizovanou výrobu a vícestrojovou obsluhu této operace.
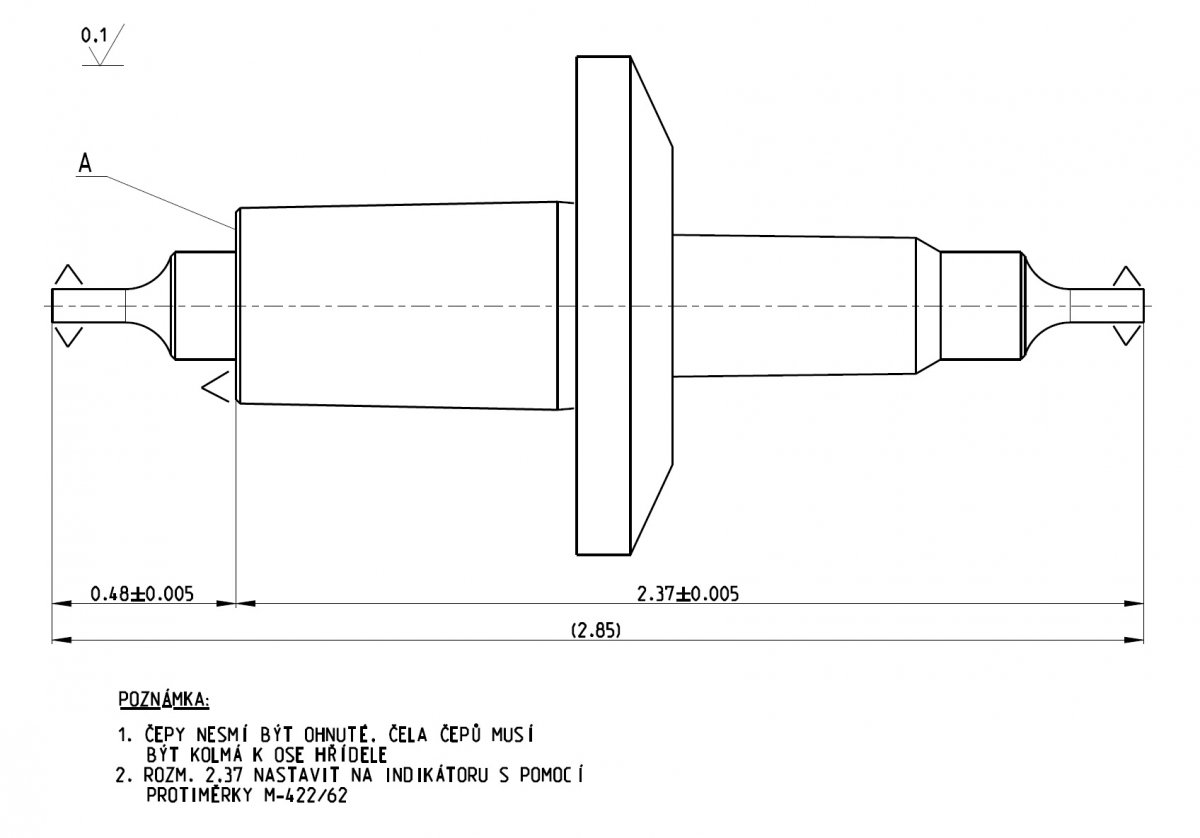
Leštění ( rolírování ) čepů
Z důvodů snížení třecích sil, prodloužení životnosti ložisek a hřídele, a zaručení udržení mazacího oleje mezi ložisky a čepy byla do technologického postupu zařazena výrobní operace – leštění trumpetkových ploch čepů hřídele.
K tomuto účelu se používala konstrukčně poměrně náročná dvouvřetenová leštička Švýcarské firmy STRAUSAK – typ STRAUSAK 119A. Leštění obou čepů probíhalo současně prostřednictvím dvou kotoučů ze slinutého karbidu se svislou osou rotace. Součást vodorovně upnutá v přípravku a otáčená mechanismem leštičky měla opracovány jak válcové plochy čepů – čely kotoučů, tak jejich přechodové části s rádiusem – obvodové plochy kotoučů. Proces leštění je znázorněn na obrázku níže staženém z webových stránek firmy STRAUSAK která, jak je vidno, princip funkce strojů, pro úpravy povrchu rotačních součástí, používá dodnes. Funkční plochy leštících kotoučů mají žlutohnědou barvu. Mezi nimi je upnuta vzorová součást, která je otáčena obvodovými plochami přitlačených disků. Přípravek nesoucí součást není znázorněn. Hodnota úběru materiálu na průměru čepu z Eltonu činí 0,005 mm, což je i hodnota uvedená v technické specifikaci výrobcem rolírovačky.
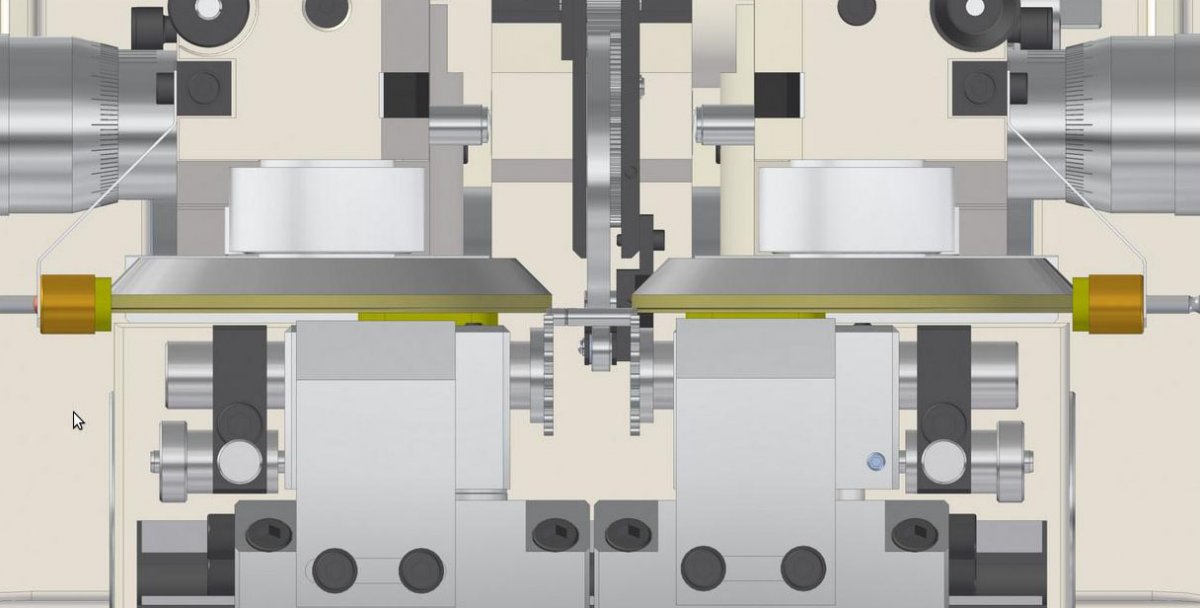
Příklad této výrobní operace názorně ukazuje, jak náročné zařízení je nezbytné vyrobit, abychom docílili požadované kvality povrchů okem téměř neviditelných ploch. Nicméně, technologie rolírování byla používaná výrobci NH ve Švýcarsku a Francii ještě před zavedením výroby NH v Československu.
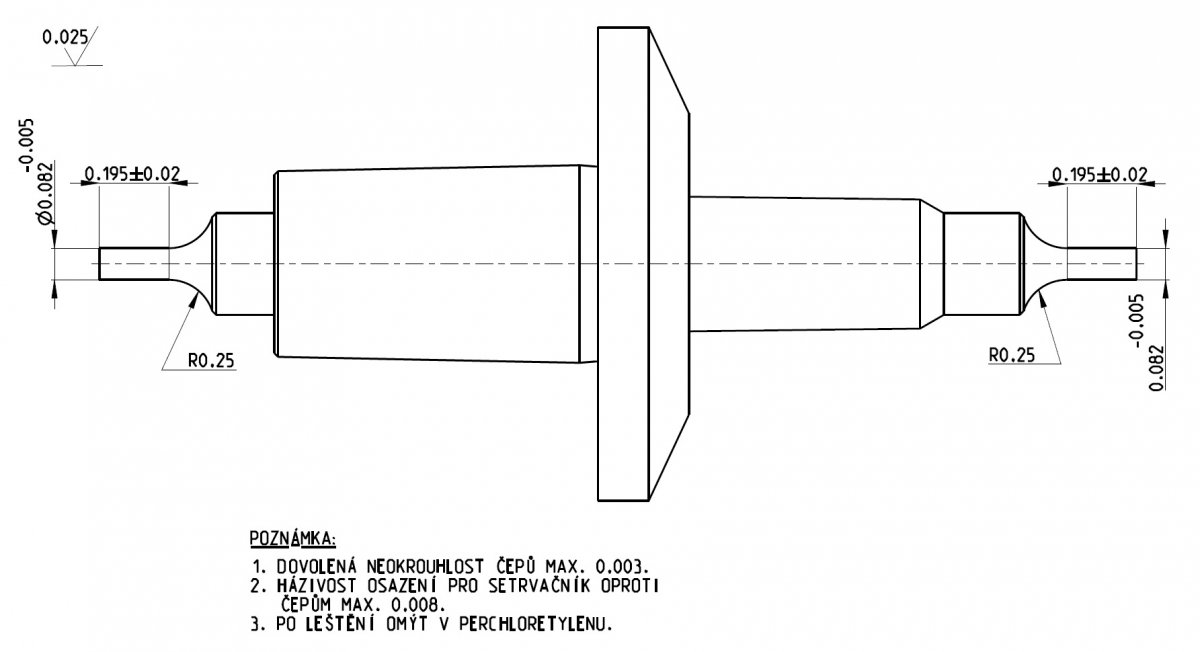
Zrcadlové leštění čepů:
Ze stejných funkčních důvodů jako bylo leštění dříků čepů bylo nutné provést leštění i jejich čel, což byla další výrobní operace vyžadující k tomuto úkonu uzpůsobený stroj. Současně s leštěním čel čepů došlo i k vytvoření rádiusu na přechodové hraně z čela do dříku, což příznivě ovlivňuje trvanlivost axiálního ložiska a opět snižuje tření při chodu. V počátcích výroby byla operace prováděna na ručních hodinářských leštičkách BOLEY. Koncem padesátých let však podnik přistoupil k vývoji leštičky vlastní, dle mého názoru, produktivitou odpovídající rostoucí výrobě NH. Funkční součástí leštičky byl otočný disk, ve kterém byly po obvodu kuželové drážky – celek velmi zjednodušeně připomínající popelník. Do drážek byly na jedné straně disku za své kuželové plochy obsluhou vsazovány hřídele, které byly unášeny pod pružící přítlačný kotouč. Ten hřídel v disku roztočil a k čelu čepu se přistavila polohovatelná miska se směsí leštící pasty o kterou byly dané partie leštěny. Složení pasty viz. poznámka na výkrese. Jelikož má hřídel dva typy kuželů a dva čepy, byly nutné i dva typy disků – každý disk umožnil opracování pouze jednoho čepu.
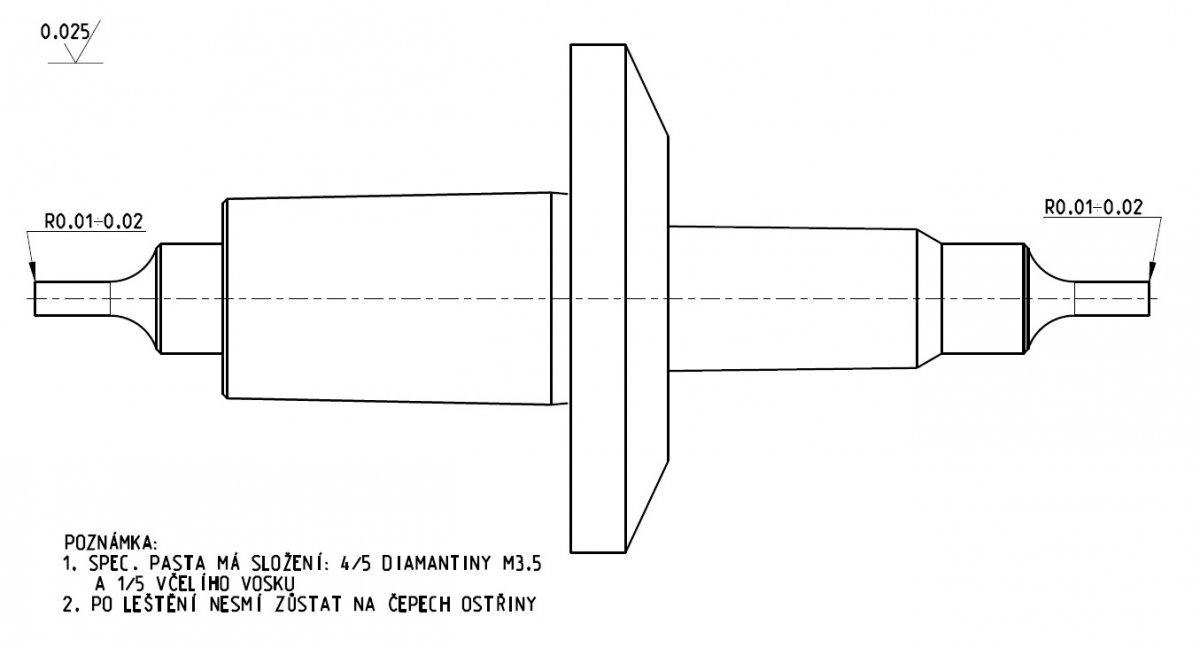
Povrchová úprava:
Hřídel setrvačky je jednou z mála komponent NH na které nebyla prováděna povrchová úprava např. niklováním, zlacením či chromováním, ale z čistě funkčních důvodů byla podrobena pasivaci. Při pasivaci je na povrch ocele nanesena mikroskopicky tenká vrstva oxidů legujících prvků, která jí chrání proti korozi a v případě aplikace na hřídel i zlepšuje tření. Před pasivací je nutné součást důkladně omýt a odmastit.
Mezi-výrobní operace:
Tento poměrně obsáhlý text zmiňuje pouze výrobní operace, při kterých dochází buď k úbytku materiálu anebo konečné povrchové úpravě součásti. Do celkového výrobního cyklu je však nutné zařadit ještě mezikroky, při kterých docházelo např. k odostření, omýlání, oplachování, kontrole, odmaštění, atd. Byť je každá z těchto činností zajímavá, a kolikrát i způsob jakým byla dotažena do své konečné podoby, není v moci tohoto příspěvku uvést vše. Cílem podniku v té době bylo jednotlivé operace co nejvíce automatizovat, zkracovat výrobní časy a zvyšovat produkci a kvalitu, což se dle autora pramenu 1, dařilo.
Zařazení položky do katalogu ND
Pro účely snazšího zajištění oprav hodinek, u kterých došlo během provozu k poruše, byl vytvořen katalog náhradních dílů vydávaný Chronotechnou. Každá součást hodinek měla v katalogu přiřazené své číslo, pod kterým ji bylo možné dohledat a objednat. Číslo hřídele setrvačky kalibru 50 je 82. Potřeboval-li opravárenský hodinářský podnik určitý počet hřídelí pro konkrétní typ strojku, pak stačilo vyplnit poměrně stručnou objednávku:
Příklad objednávky:
... ( adresa )
100 kusů hřídele setrvačky č. 82 pro náramkové hodinky PRIM, typ strojku 011
Autor textu: Tomáš Faktor
Použité prameny:
1, VAJSAR, Jaroslav: Technologie náramkových hodinek Prim vyráběných v Novém Městě nad Metují v letech 1954 – 1986, Nové Město nad Metují, 2005
2, HOVORKA, Libor: Hodinky Prim 1954 – 1994, Technické muzeum v Brně, 2014
3, CHRONOTECHNA: Náhradní díly, N.P. Šternberk – závod 02 Nové Město nad Metují
4, LEINVEBER, Jan; ŘASA, Jaroslav; VÁVRA, Pavel: Strojnické tabulky, Scientia 1998
5, Vebové stránky společnosti STRAUSAK